Exceeding the Needs of the Steel Industry
Patent Pending Plasma Marking Torch Holder
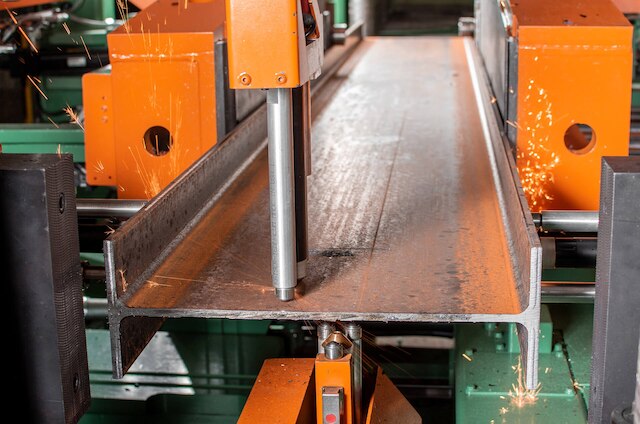
Torch assemblies that utilize a plasma marking unit operate completely independent X, Y and Z motions with ball screw feed systems.
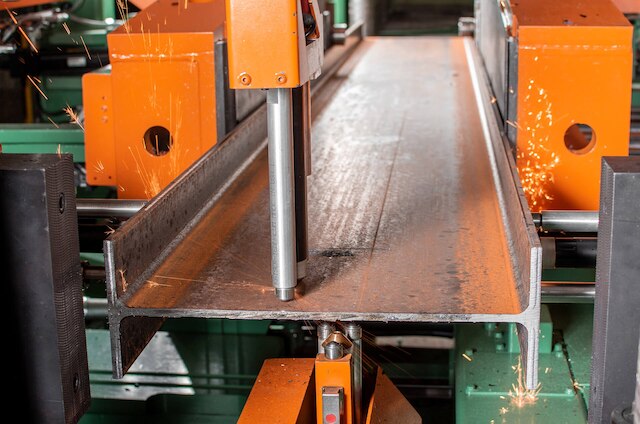
Patented Double Torch Cutting Assembly
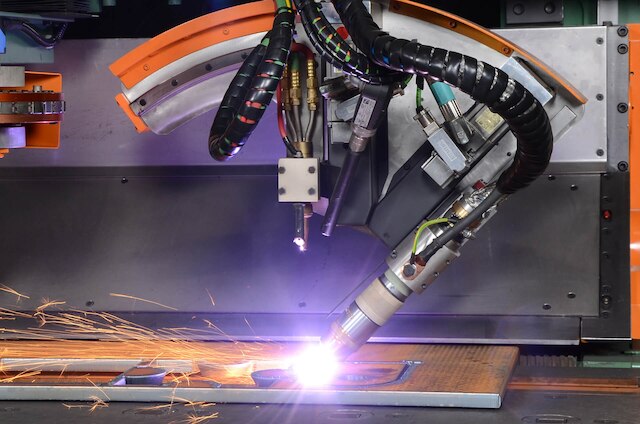
Unlike gantry style systems, the CNC plate processor design of Peddinghaus drives material to the operating area of the machine as opposed to bringing the operating area of the machine to material. This plate beveling technology is designed so that both the plasma and oxy-fuel cutting torch of the machine can utilize beveling capabilities with the application of a single cutting assembly.
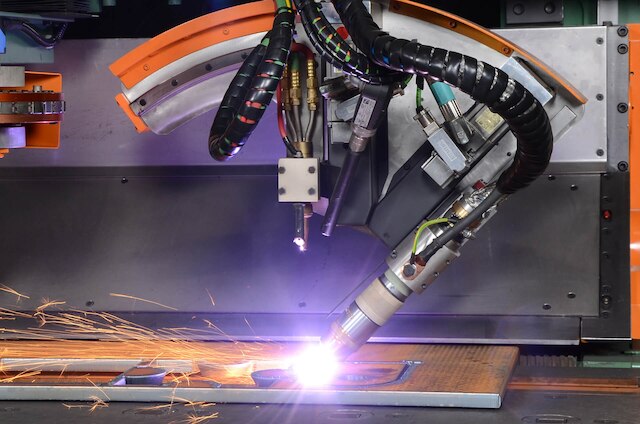
Innovative Roller Feed Measurement
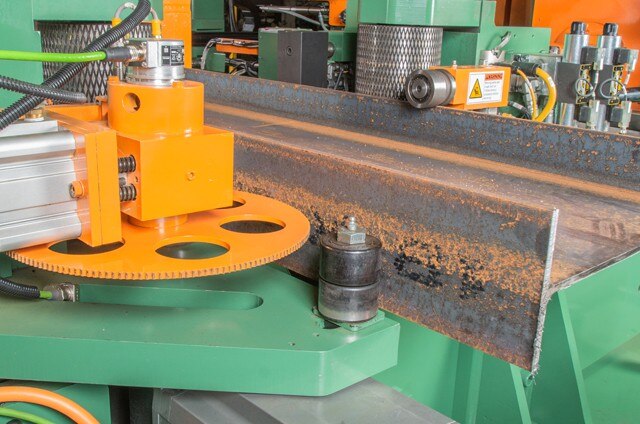
As accurate as measuring material can be, the Roller Feed drive and measurement system from Peddinghaus is designed to improve accuracy even greater than before. Steel can pass through piece after piece with no stop in production. The Roller Feed is designed to maximize contact with the material which helps eliminate errors.
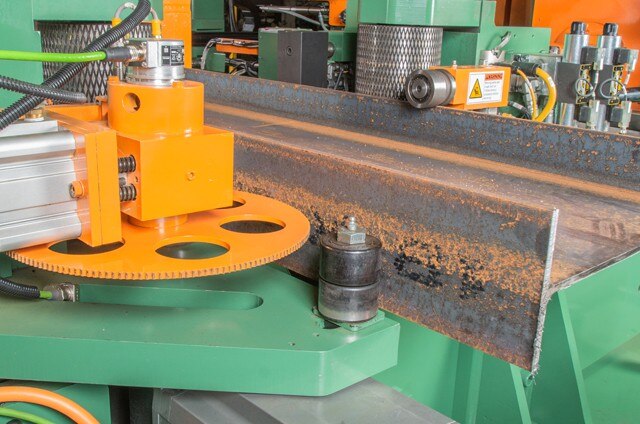
Aggressive Drilling Process
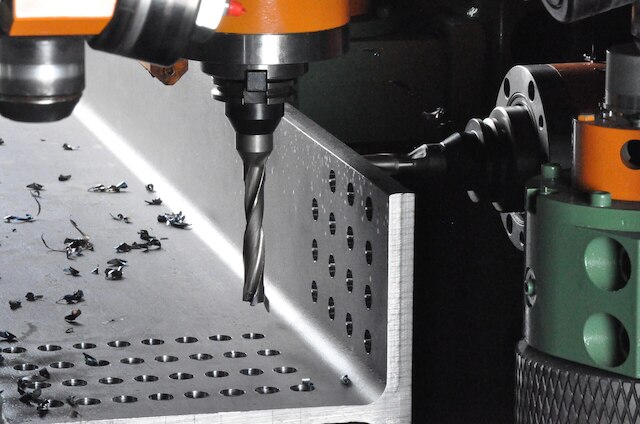
Peddinghaus drill lines utilize Siemens electronics to achieve industry-leading hole times. The high-horsepower spindles also have high torque. This allows the carbide drills to remove more material with each rotation. A thicker, more aggressive cut on each pass will decrease drilling time and part completion time.
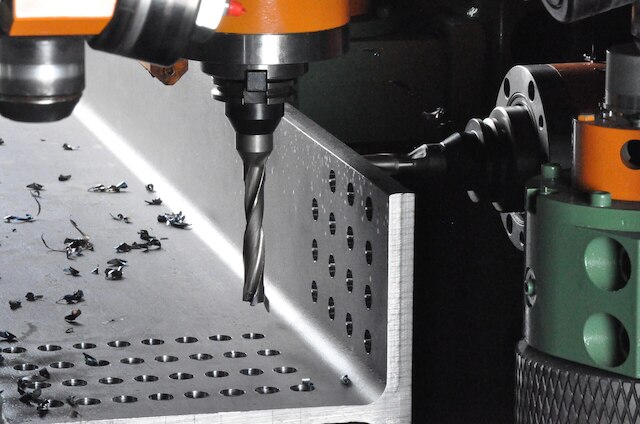
3D Profile Scanning System
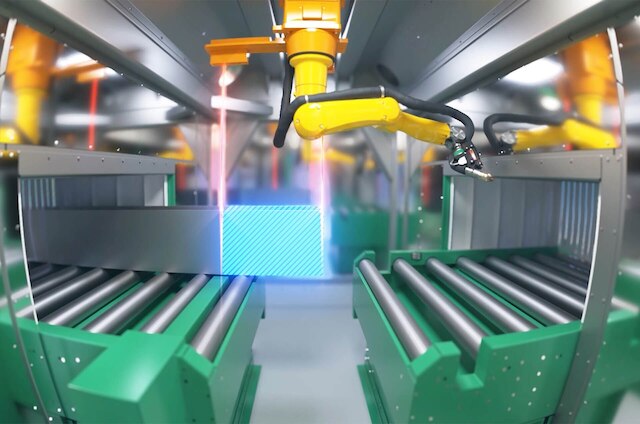
This state-of-the-art measurement system detects positional displacement and distortions of material. The intelligent system consists of a triangulation laser scanner for measuring sections. Material scanning is executed inside the cutting area and is performed in one, continuous cycle.
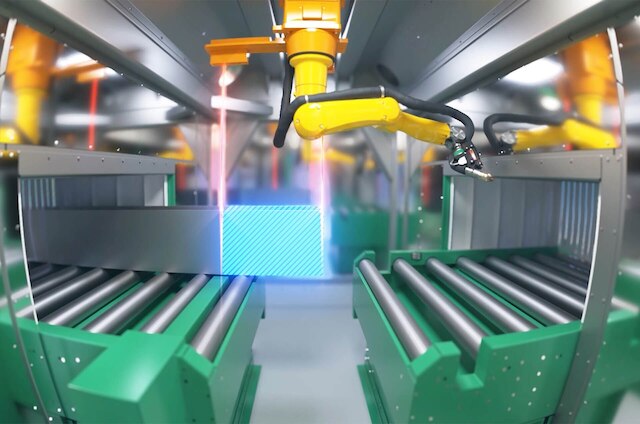
Speed Sawing Technology
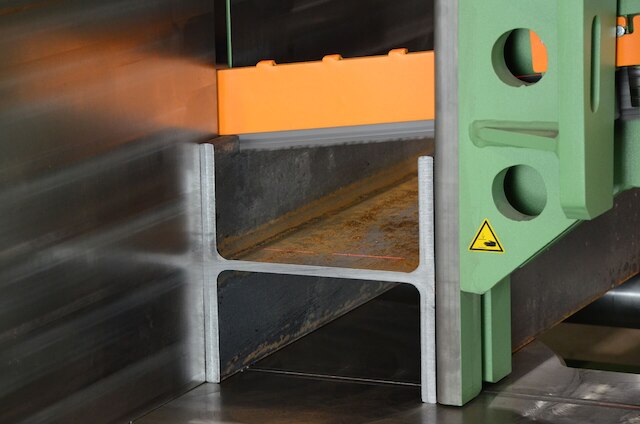
Reduce cut times and increase productivity with these saw features: rapid advance blade approach, automatic material sensing, automatic cutting speed transition, feed compensation during the cut, end of cut sensing and automatic retract.
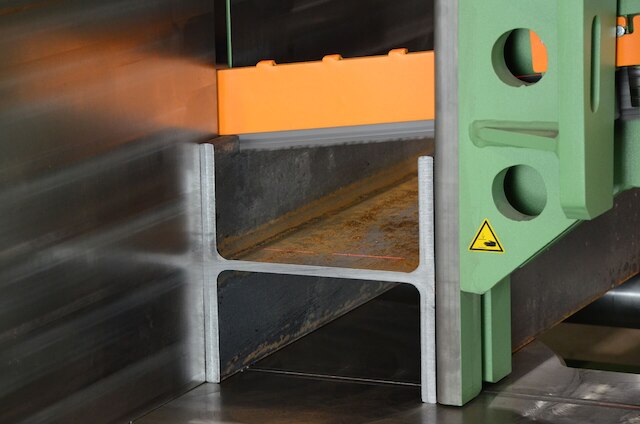
SignoMat Adjustable Character Stamp
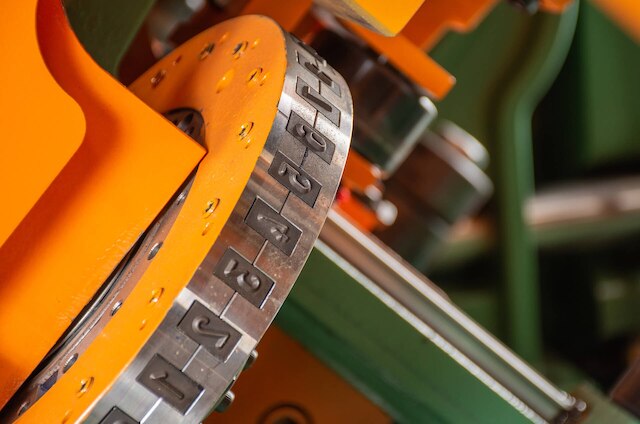
SignoMat part stamping is the high speed part marking alternative to carbide scribing. This hard stamping option will hold up to 36 characters, letters or numbers. These characters are stamped to a depth of 1/32” (.8 mm) and at multiple heights of 1/4” (6 mm),1/2” (12 mm), 5/8” (15 mm) and 3/4” (19 mm).The stamping speed is a swift rate of 1 character per second.
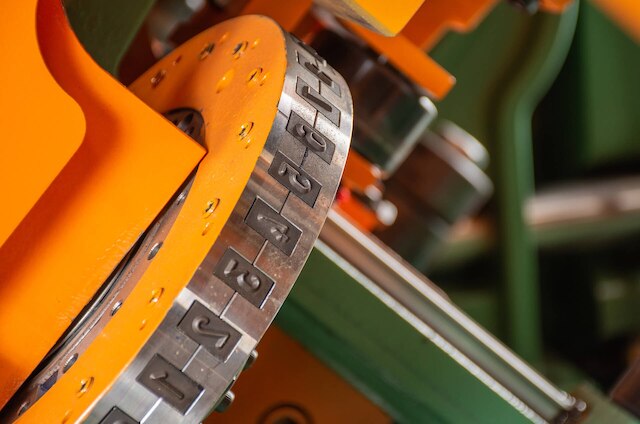