Doherty Steel, Inc: Laying a New Foundation
PeddiNews: Issue 66
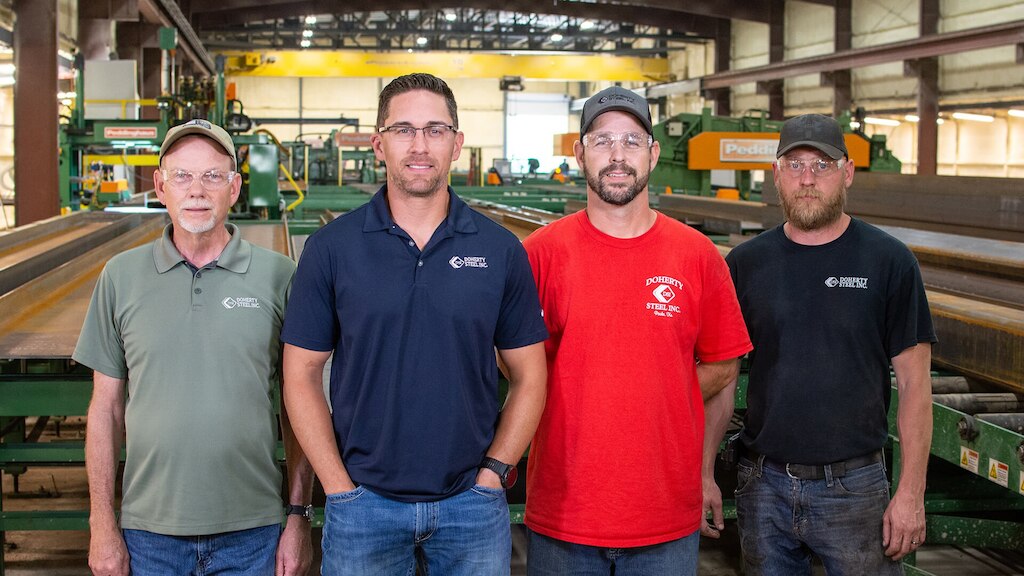
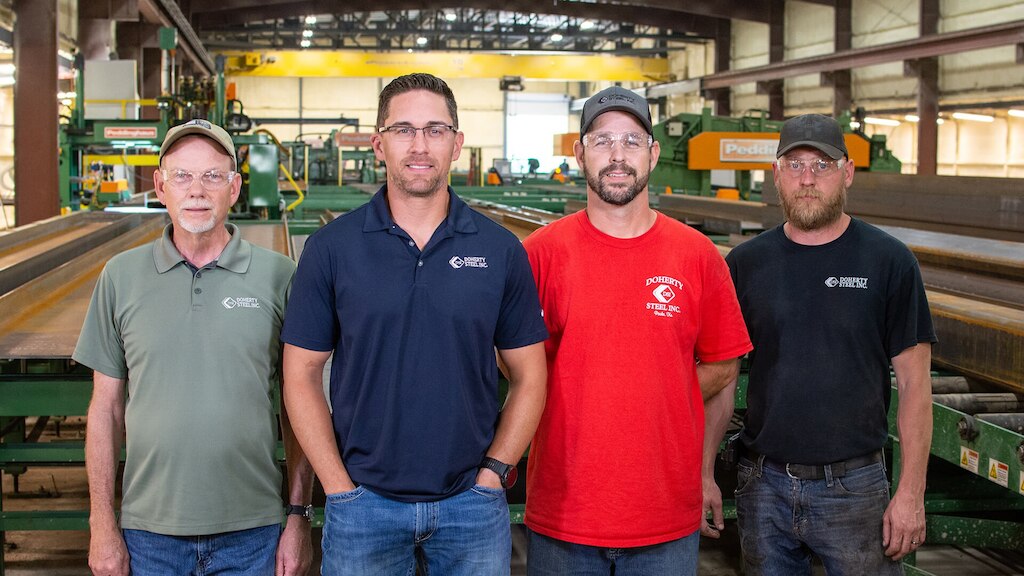
The Doherty name has long been associated with American structural steel fabrication. In 1959, James Doherty established what would later become Doherty Steel in his parent's garage. Like many fabricators, his early work in ornamental iron led him down the path of structural steel. Once steel is in your family bloodline, it tends to strengthen from generation to generation like each steel beam added to the frame of a building.
By just 12 years of age, little Dennis Doherty was helping out in the shop. Dennis, current President of the company recalls, “I remember sitting in the window of my bedroom watching my dad weld in my grandpa’s garage at 2:00 in the morning. After long, I was helping him in the shop cutting beams with a torch. That’s how it all started. We would eat, sleep and breathe steel!”
Dennis continues, “I followed suit by bringing my own kids here in the summertime to help out and learn the business. I’m pretty proud of that because they are quite talented and have transformed this company into what it is today.”
Chance Doherty’s early start out in the shop with his father gave him the upper hand in learning the core principles of steel construction, structural steel fabrication and overall business strategy. By blending his knowledge of the family business with his understanding of modern technology, Chance has used his ambition to put Doherty Steel on a whole new level. Now Vice President of the company, Chance is determined to honor his family legacy by leaving behind something remarkable for the next generation, “Doherty Steel means everything to me. As the third generation of our family business, I feel like I owe it to my grandparents and our team to keep this place going strong.”
32,000 Square Foot Upgrade
Over the years Doherty Steel has transformed into a full-service kind of business. Not only do they estimate, design, project manage, fabricate, ship and erect - they’re by the customer’s side until the full project scope is completed. Because of Doherty’s reputation for providing customers with high-quality structural steel fabrication and erection practices on time and within budget, they decided to rethink and rebuild the shop with the goal of increasing tonnage to accommodate those loyal, repeat customers. Now they’re moving some serious material.
“In the past year we doubled our processing equipment, adding 12 machines, 1,471 ft (448 M) of conveyors and 32,000-sq-ft (2,973-sq M) of floor space to our facility to cover our bases for all projects,” Chance declares. “I love the new setup we have. We have 75 ft (23 M) of material handling to stage and load members at the start of production. First, the PeddiWriter marks all saw cuts, plates, piece marks and layout marks. From there, material is filtered in through two drill/saw lines depending on the size of the material. We have a “heavy” side and a “light” side. On the heavy side, material gets cut on a DG-1250 band saw before being drilled on the BDL-1250/9D drill line. Running parallel to the heavy side, material flows through a second DG-1250 for cutting, followed by drilling on our Advantage-2 on the light side.”
“We actually added a 3rd saw outside of the drills that we use for multiparts to keep our main lines free. We never backfeed material through the system. After the material is sawed it flows to our two ABCM-1250 copers for block outs and full pen weld preps. From there, material is fed to either our cambering machine or PeddiBlast before it gets sent off to the fabrication bay. I like to think we have a full processing system here to cut raw material, put holes in it and lay it out - we have everything we need now.”
The Method Behind the Machinery
Before commissioning their new line of Peddinghaus equipment, beams wider than 40” (1016 mm) could only be processed by hand, limiting their capacity. Knowing the level of difficulty involved in high-volume manual fabrication, Doherty used to shy away from large projects. Today, they welcome large projects with excitement because that limitation has been resolved. “We’ve never had the capacity to run anything over 40” until now,” Chance states. “We recently ran our first 44” beam, which was a big deal because it used to be so tedious. We couldn’t even put the material up on our rollers, so we had to bring it in and hand cut it all. Now we just load it and run it. It was all processed with ease from beginning to end.”
Patrick McCorquodale, Shop Superintendent, adds, “I’m pumped that we can run 44” beams through here. For years we dealt with bringing it into the shop to be cut and drilled by hand. Now that we have the new line, we’re saving a ton of time! It’s nice to be able to process a 44x500 beam while having a second line running simultaneously.”
The new system has led to a productivity explosion at Doherty and continues to offer unlimited potential. Historically, Doherty has been able to push an impressive 10,000-15,000 tons out of the shop each year. This year, they expect to hit 20,000-25,000 annual tons. Next year, they expect a total ROI. According to Patrick, “The new system did not require us to hire any more operators. With the way our drill lines are set up, we only need one of our guys to operate both systems. It helps that our employees are excited and totally on board with the new technology. They genuinely want to see this system succeed.”
Fully-Operational Installation
An entire shop overhaul to this scale requires a lot of planning, and remaining profitable during the installation process can pose a challenge. Doherty’s installation required a strategic approach, and with the help of their dedicated employees and Peddinghaus service technicians, the shop was able to remain operational the whole time.
Chance explains, “We just installed a LOT of equipment. Our original processing line was at the north end of the facility, so we were able to keep that up and running while we essentially remodeled and added onto our previous storage facility. So what used to be indoor steel storage has been moved outside to make room for the new processing line. That allowed us to keep up and running while we focused on the light side. Once all the machinery for the light side was operational, we were able to flip off our old system and have the exact same capacity as we had before on the new system. Then we were able to get some of our old equipment out and focus on installing the heavy side. The installation went without complications.”
When Doherty chose to rebuild their shop, they relied on fabrication expertise from Peddinghaus' Regional Sales Manager, Paul Muraski. Working hand-in-hand with Chance, the Doherty layout plan was executed to perfection. “We worked with Paul and Peddinghaus’ layout engineers to make something that I’ve thought about for years come to life. For 10 years I went through my notebook drawings over and over again knowing that this would eventually be my goal. Together we turned a vision into reality.”
A Fresh Take on the Family Business
The changes that have happened at Doherty Steel have allowed them to grow with the industry. Chance tells us, “I was the new school coming into the old school idea that no machine can outwork a man. So I had a hand in persuading everyone why we needed to trust the equipment and become more automated. After installing the equipment, everyone saw how efficient it made us in an instant.”
By acting on intuition and a commitment to the family business, Chance and his team have been able to capitalize on a solid foundation and a vision. Together, they strive to maintain the values of the company while keeping up with the needs of their valued customers who have helped catapult Doherty Steel into what it is today. Looking ahead, there is no ceiling to Doherty’s future.
Enter Today for a Chance to Win FREE Machinery
Gift cards and other Peddinghaus merchandise included
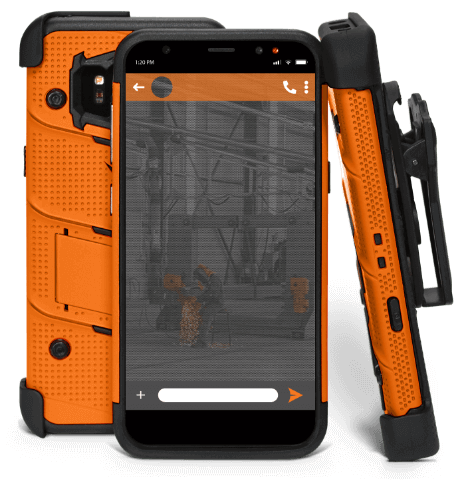
46331 mobile
TO
46331
WINNER
Normal text message rates apply. Text “STOP” to opt out. Text “HELP” for help. Up to 3 msgs / month. Terms https://www.peddinghaus.com/terms/1